Progetti
Industrializzazione di un ossigenatore per biomedicale
Nel mondo biomedicale l’attenzione per la qualità e la ricerca della competitività vanno di pari passo: questi due elementi hanno costituito le linee guida per un progetto finalizzato alla produzione di 40 diversi particolari di un ossigenatore per cardiochirurgia, da produrre utilizzando al meglio gli impianti disponibili.
Obiettivo:
- Industrializzare i 40 componenti di un ossigenatore per cardiochirurgia ottimizzando l’uso delle presse ad inizione esistenti.
- Validare il prodotto e il processo prima del trasferimento delle attrezzature.
- Garanzia dei tempi sul progetto totale
Attività:
- Ottimizzazione prodotto/processo (stampabilità, eliminazione criticità).
- Individuazione di scenari alternativi di configurazione stampi.
- Costruzione stampi.
- Certificazione prodotto e processo.
Ottimizzazione prodotto/processo e industrializzazione
L’assoluta precisione dei prodotti in termini di geometria e stabilità dimensionale è un fattore chiave in un settore così delicato come il biomedicale.
Lavorare in maniera preventiva sulla geometria dei prodotti per ampliare la finestra di stampaggio e rendere quindi più affidabile il processo è stato un elemento fondamentale per il successo del progetto.
La necessità del cliente era quella di produrre 400.000 ossigenatori l’anno, ciascun prodotto essendo costituito da 40 particolari in PC da produrre su un parco presse con tonnellaggio a 60 ÷ 350 ton.
Sono state analizzate da un punto di vista tecnico/economico diverse configurazioni (stampi multi-cavità a libro o in piano), scegliendo alla fine quella più efficiente rispetto al parco presse disponibile: 35 stampi per la realizzazione dei 40 componenti.
Importanza della qualità
Dopo aver individuato la configurazione dei 35 stampi, il focus si è spostato sulla qualità degli stessi, considerando che in questo caso essa è fortemente correlata alla funzionalità di un prodotto tanto delicato. L’accuratezza delle lavorazioni per garantire la pulizia e precisione delle superfici e la stabilità dimensionale delle zone di interfaccia hanno costituito fattore chiave di successo del progetto.
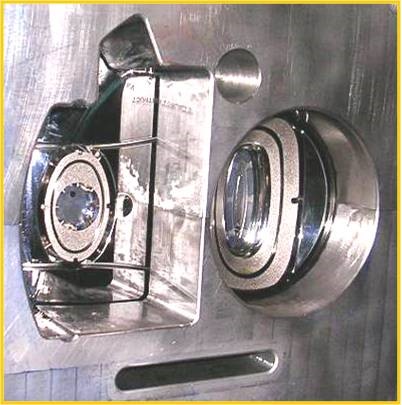
Validazione e omologazione
La procedura di validazione in ha richiesto:
- Cp,Cpk required
- SPC dimensions
- validation according to GMP (IQ,OQ,PQ)
Per ogni stampo sono stati eseguiti:
- Mould test through the Factory Acceptance Test (FAT) :
- functional test
- parameters set-up starting from MoldFlow inputs
- long run à wide sampling for long term capability evaluation recording process data through cavity pressure sensors
- moulding window investigation defining three moulding parameters settings (A,B,C)
Accuratezza e velocità
Nonostante la delicatezza del progetto e l’elevata accuratezza richiesta in ogni sua fase il coordinamento come unico partner del cliente ha consentito di passare dal project start (feasibility analysis) al SOP presso lo stabilimento di produzione in soli 15 mesi.
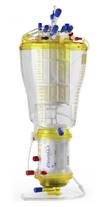